こんな課題はありませんか
- 工場を自動化することで、省人化を進めたい
- 生産ラインにおいて、新設・更新・改造を検討している
- 海外に生産ラインを新設、あるいは国内の工場を移設したい
- 生産技術の観点から、生産ラインの計画を再検討したい
国内外の生産ラインの計画・プロセス、レイアウト、仕様作成・設計、調達(製作・購入)・輸送、据付指導・立ち上げ支援、保守までをトータルでサポートします。自動化・省人化に対しては、工場全体の生産・物流の自動化計画から、個別装置の基本設計・詳細設計・設備納入まで、トータルに支援します。放射線環境・クリーンルームに対応するFA設備にも実績があります。そのほか、3次元設計、ロボットシミュレーション、物流シミュレーションなどを活用することで、実現性を確保しています。
国内外の多様なお客様との業務経験をもとに、以下のようなサービスをトータルに、もしくは個別に行っています。
- 自動車生産工場計画・フィージビリティースタディー
- 新規・改造・混流など、様々な条件下のプロセス検討・レイアウト作成
- 物流自動化検討
- 車体・車両設計の生産性REVIEW(SE)
- 設備引き合い用仕様書作成
- 設備調達・トライ・輸送
- 据付指導・管理
- 立ち上げ支援
SHOPは主に、車体・組立を対象にしていますが、プレス・塗装も実績があります。
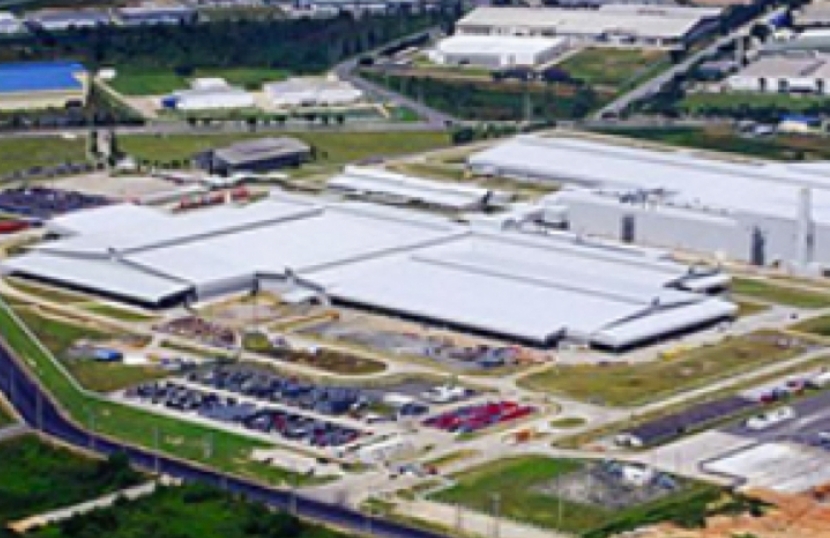
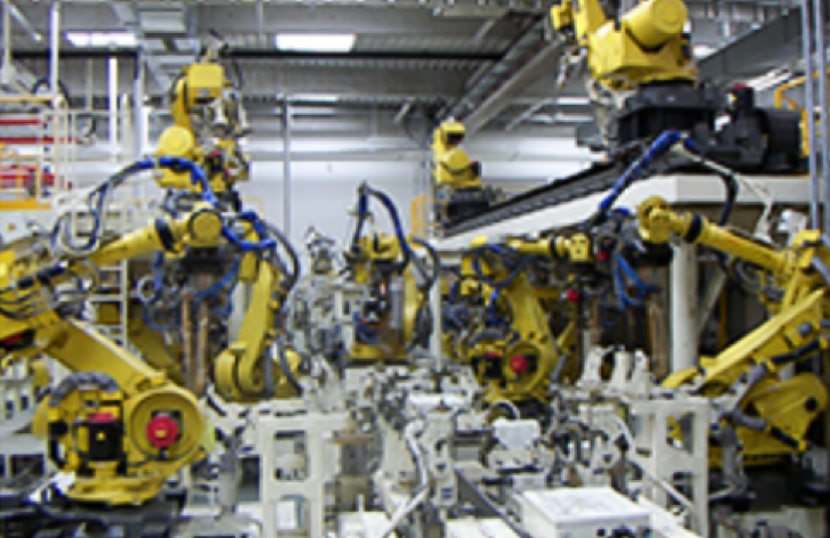
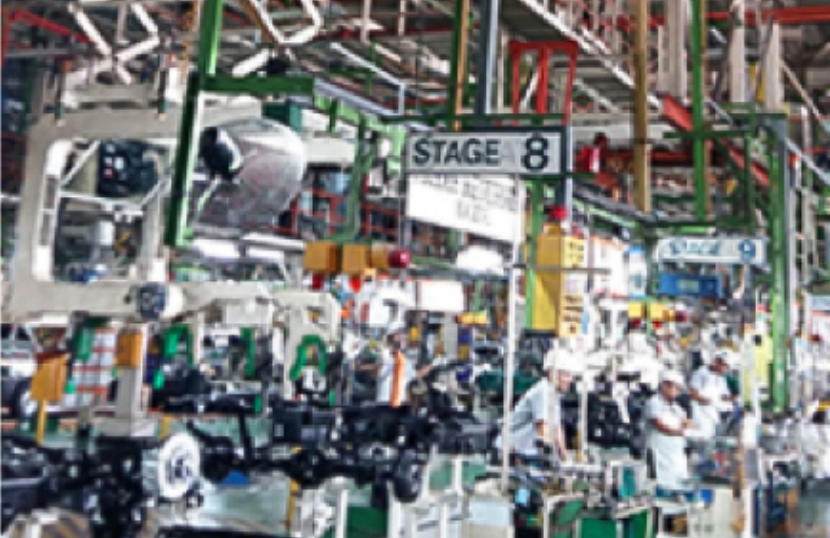
自動車産業への支援で培った知見を活かし、その他の産業分野に向けて、エンジニアリング業務・自動化を中心としたサービスを展開しています。たとえば、自動車部品、建設機械・農機、医薬など、さまざまな分野において量産工場や試作工場へのサービスを提供しています。
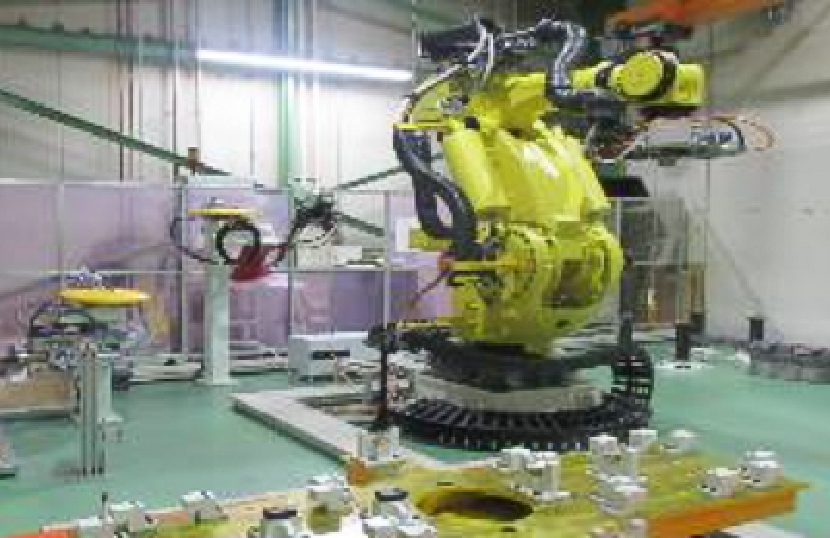
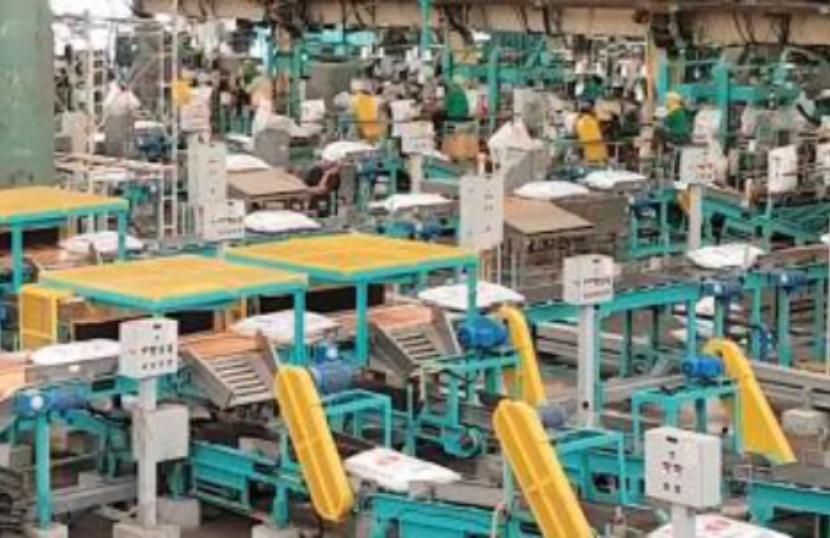
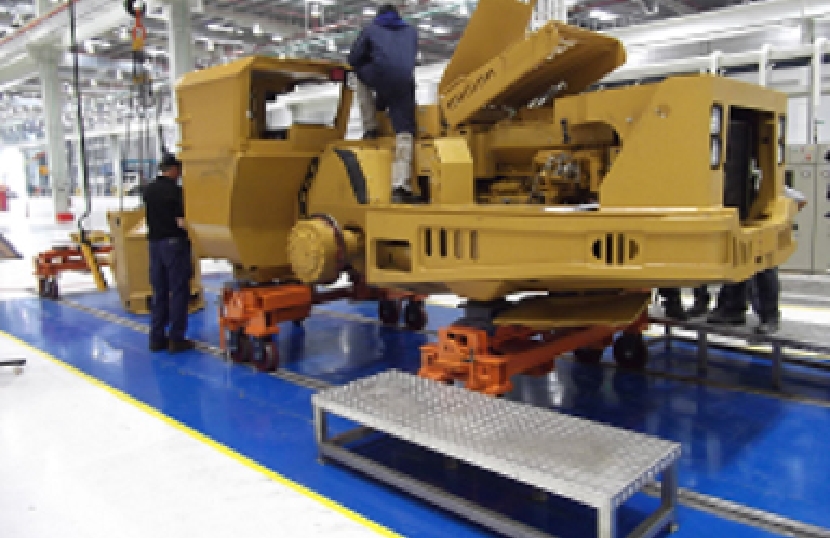
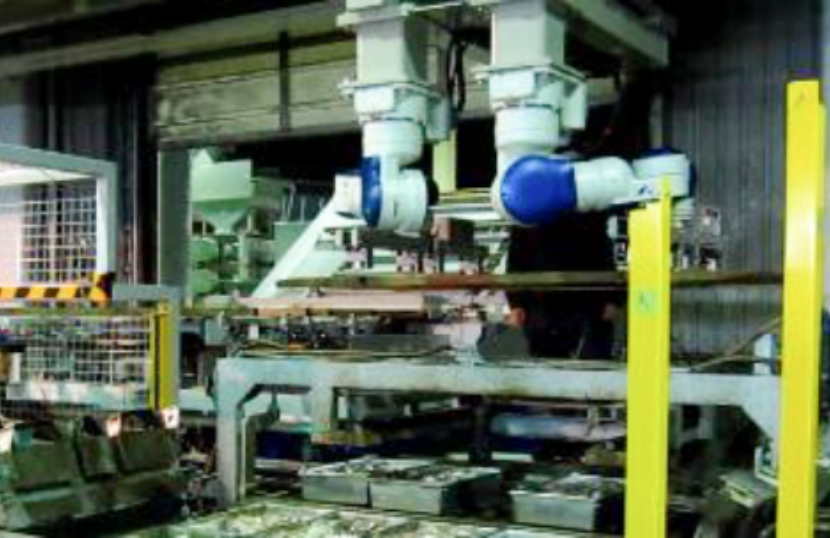
半導体、医療、原子力など、クリーンルームや放射線環境で使用するFA設備を数多く手がけてきました。クラス1のクリーン度を要求される半導体製造のウエハ搬送装置やその周辺設備をはじめ、精密電子部品組立・検査装置や医療機器など、必要とされるクリーン度を満足する設備の設計製作で、数多くの実績を重ねています。
また、最もきびしい品質条件が要求される原子力発電関連の周辺自動化設備の開発では、燃料製造設備をはじめ放射性廃棄物処理設備など、概念設計にはじまり、基本設計・詳細設計を経て、実施設計や製作まで、高い品質要求を常にクリアして信頼にお応えしています。
生産現場における部品組み立てから検査・梱包ラインまで、トータルエンジニアリングを支援することにより、お客様の生産ラインや工程の自動化に貢献します。自動車工場のエンジニアリング業務で培ったロボット適用性検討技術、社内に所有している検証用協働ロボットの活用など、状況に合わせた最適な自動化提案を行い、設計から設備調達・据付・運転立ち上げまでを一貫してサポートしています。
生産ラインの検討から稼働まで、お客様と二人三脚で成功に導きます。
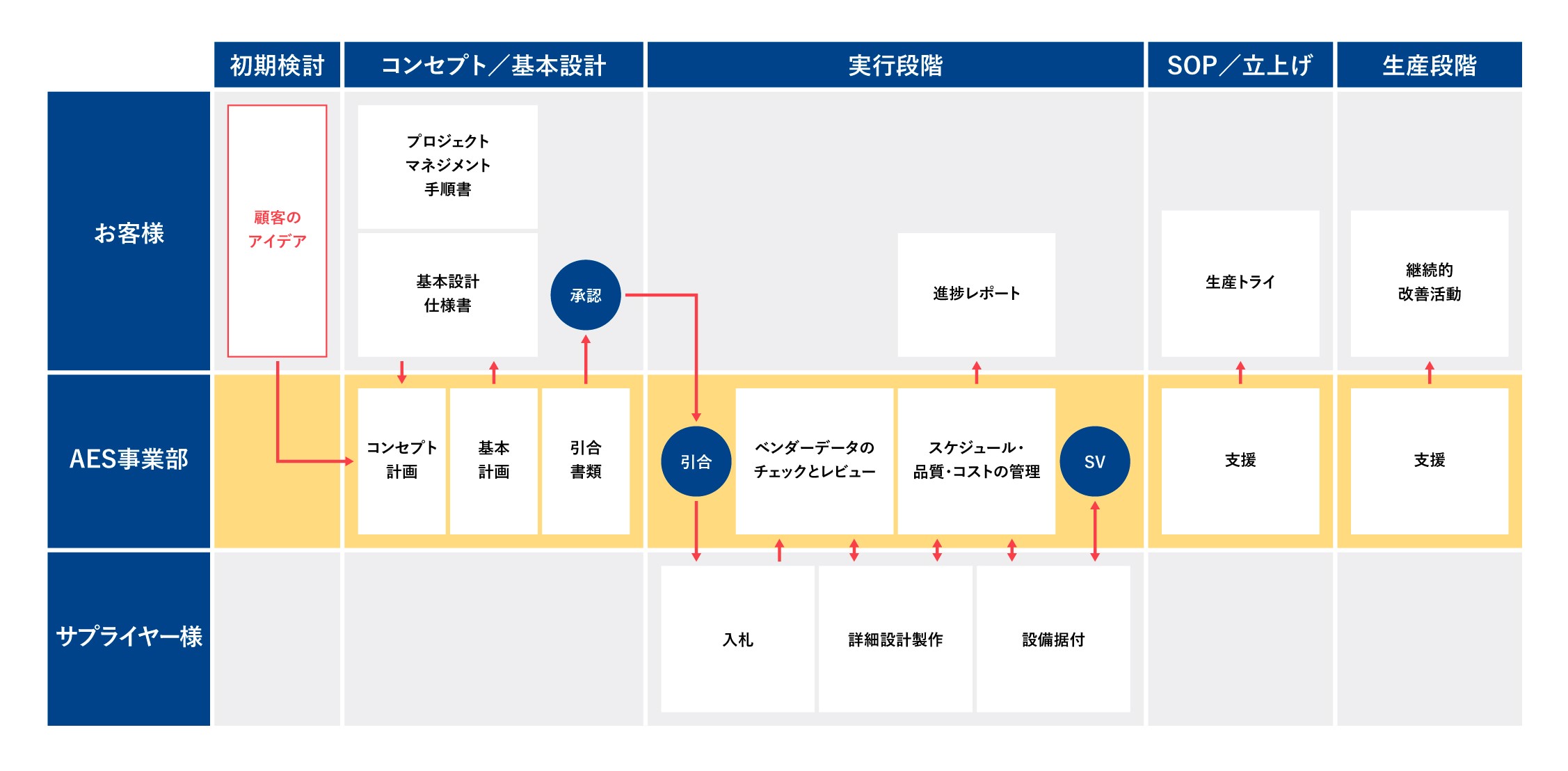
自動車・一般産機
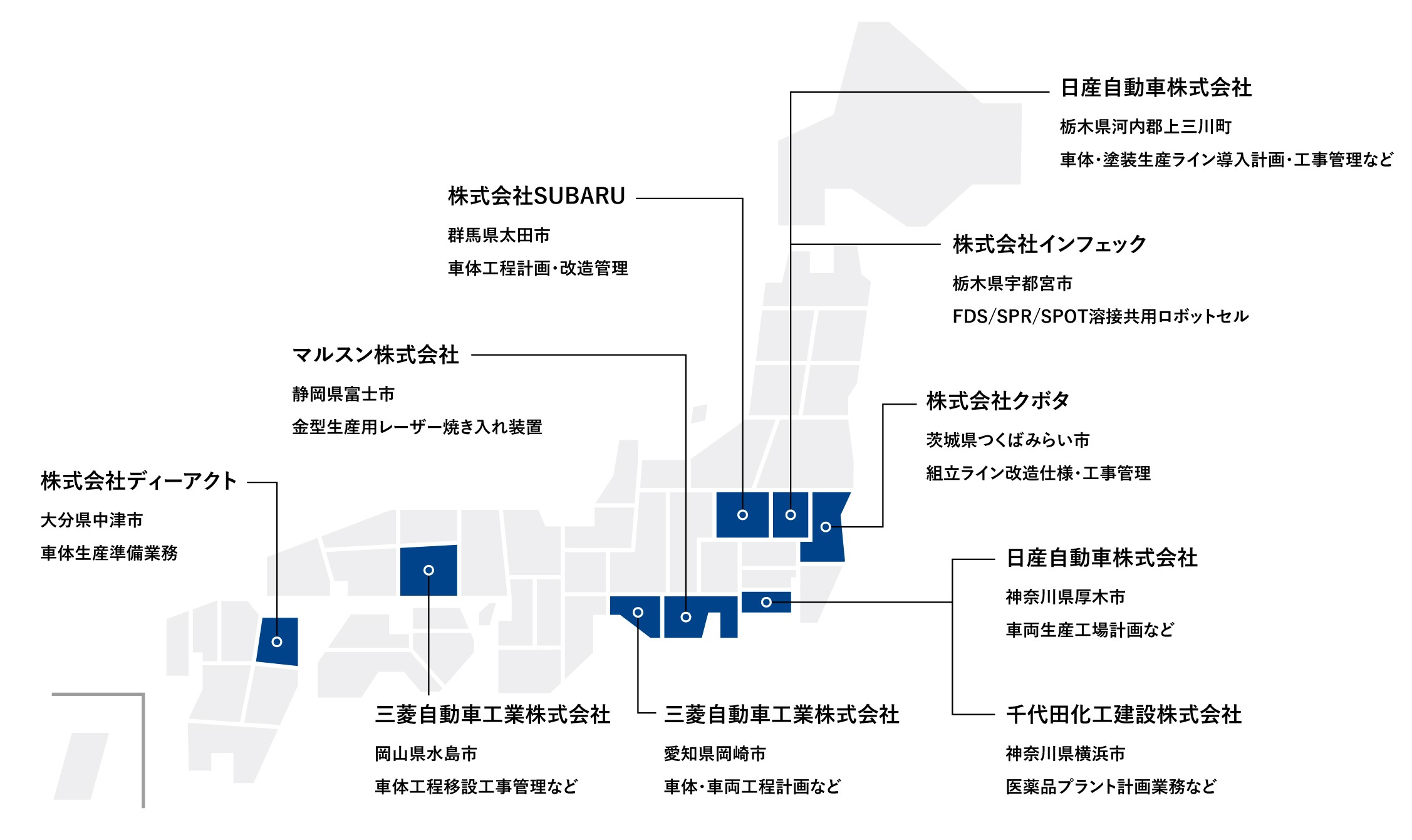
特殊環境
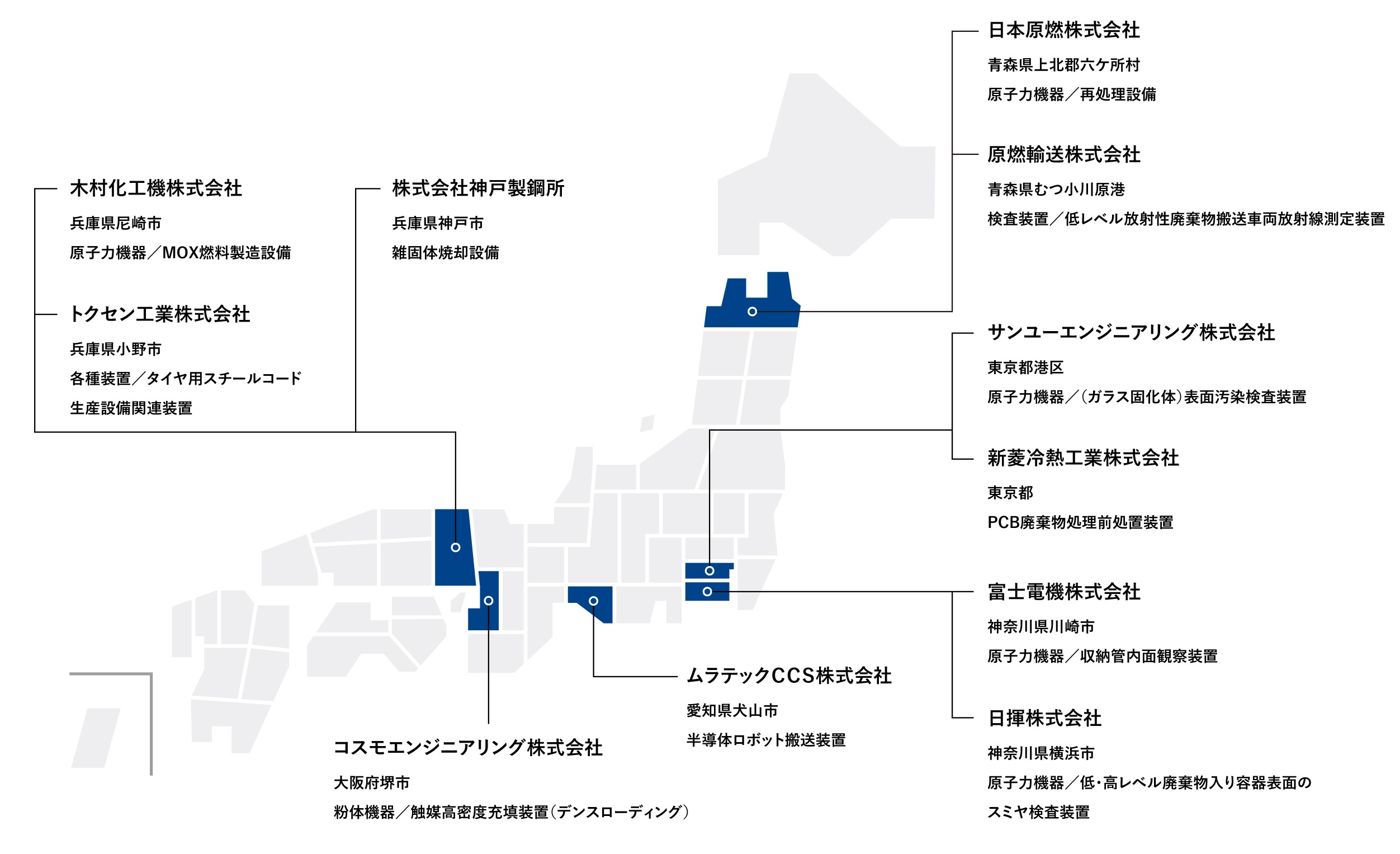
自動車・一般産機
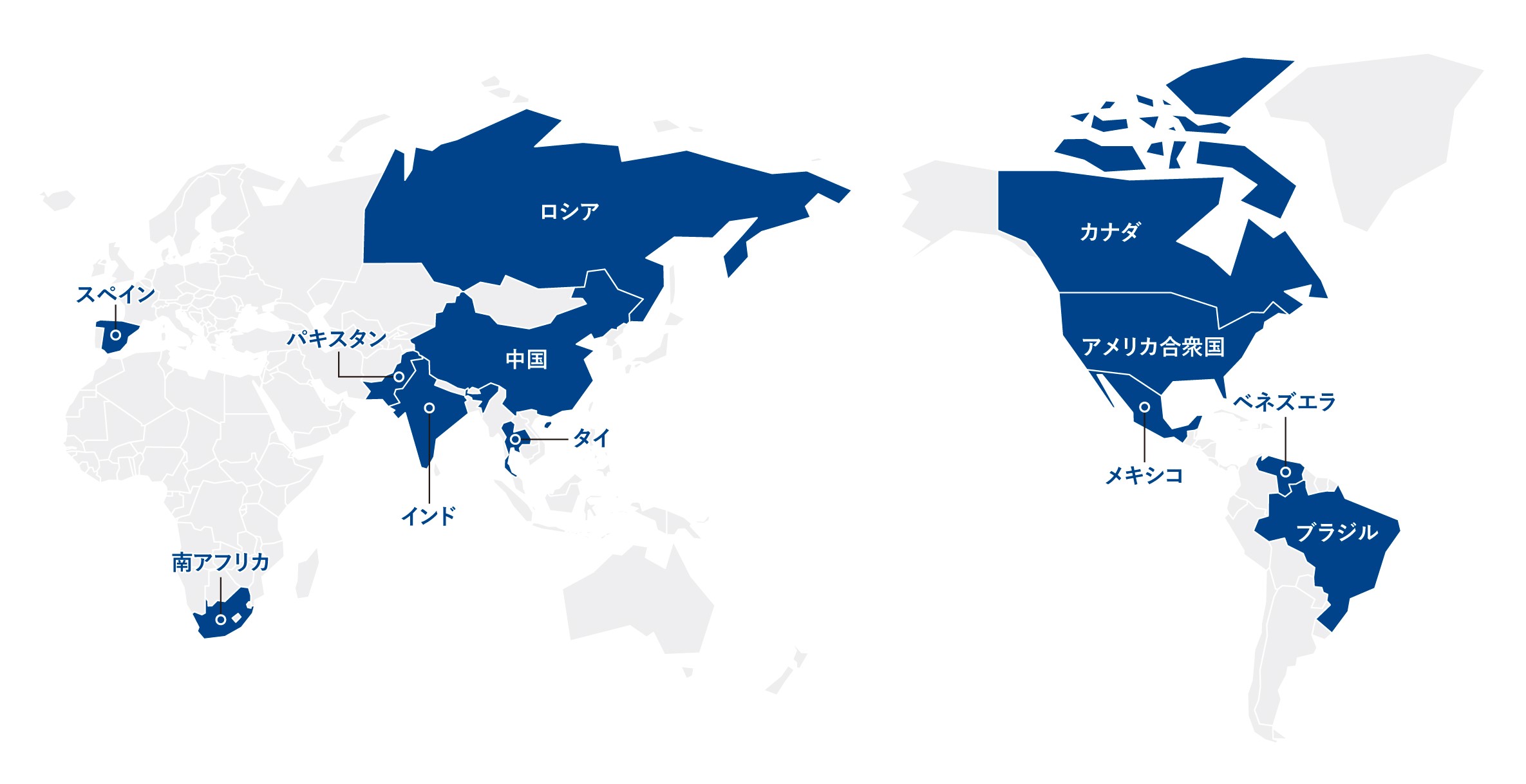
自動車・一般産業
■自動車製造・自動車部品・自動車設備
(国内)
- いすゞ自動車株式会社
- 株式会社SUBARU
- ダイハツ工業株式会社
- 株式会社ダイフク
- 日産自動車株式会社
- 日産トレーディング株式会社
- 株式会社ホンダトレーディング
- 三菱自動車工業株式会社
(海外)
- BYD AUTO
- Ford Thailand Manufacturing
- Mahindra & Mahindra Limited
- Motherson Automotive Technology & Engineering
- Renault Nissan Automotive India Private Limited
- Tata Motors Limited
- SAIC-GM
■一般産業・その他
(国内)
- 川崎車両株式会社
- 千代田化工建設株式会社
- 株式会社ニッピ
(海外)
- Caterpillar (Thailand) Ltd.
- Caterpillar India Private Limited
- India Metal One Steel Plate Processing Private Limited
特殊環境機械
■FA機器(産業機械設備)
- パナソニック ホールディングス株式会社
- 三菱電機株式会社
- 株式会社高田工業所
- トヨタ自動車株式会社
- 本田技研工業株式会社
- 株式会社アイシン
- 株式会社トクセンエンジニアリング
■半導体、液晶製造関連機器
- ムラテックCCS株式会社
- 東レエンジニアリング株式会社
■医療関連機器
- シスメックス株式会社
- 参天製薬株式会社
- 藤沢薬品株式会社
■原子力設備・機器
- 核燃料サイクル開発機構
- 日本原燃株式会社
- 木村化工機株式会社
- 富士電機株式会社
- 新菱冷熱工業株式会社
- 原子燃料工業株式会社
- 株式会社神戸製鋼所
- 日揮株式会社
- 原燃輸送株式会社
- 三菱マテリアルテクノ株式会社
- サンユーエンジニアリング株式会社
- 国内電力各社
■情報・AV家電
- PHC株式会社
完成車メーカーの自動車を海外(中央アジア)でノックダウン生産する計画の実現。
敷地内への各ショップビルディングの配置から始まり、各ショップ内の概略レイアウト、必要設備の洗い出しなどFeasibility Studyを実施した。完了後、設備の詳細計画、製作メーカー管理、設置管理、立ち上げ支援までを実施した。
全く構造の異なる乗用車2種と商用車1種が初期生産車種として定められていたため、ラインが共用化できる部分と専用化する必要がある部分を判断し、工程計画を行なった。
コンプリートノックダウンであるため、溶接、塗装(*)、組立各ショップがあり、それぞれの基本計画および建屋への要件定義を行なった。
ノックダウン単位、生産車種情報から各必要設備の情報を洗い出し、仕様を作製。
選定された設備設計製作は海外メーカーが多かったが、その設計図面レビュー、製作・スケジュール管理と、現地での設置指導を行なった。
*塗装ショップ計画については協力会社と共同で実施した。
Feasibility Studyレポート、設備リスト、詳細レイアウト、ユーティリティー消費表、設備仕様書(一部設備)、図面レビュー結果、設置管理レポート
当初計画通りに工場立ち上げ完了した。
2車種、3モデルの自動+手動溶接ラインの移設に伴う業務。(1万平米)
<業務範囲>
(工事開始前)
移設設備調査、移設先レイアウト検討・作成、移設先工場干渉物撤去指示、移設機器リスト作成、フロアーマーキング図作成、分解ポイント確認、分解マーキング仕様作成・マーキング作業確認、移設手順・日程作成、工事業者向け作業説明、移設先ユーティリティー接続仕様・接続位置作成、アンカーボルトリスト作成
(工事開始後)
フロアーマーキング寸法確認・修正指示、工事手順指導、進捗管理、設置位置確認、復元工事結果確認、ユーティリティー接続工事確認、改造指示書作成・工事結果フォロー
移設先のトラス高さが現状エリアよりもかなり低くなるため、高所溶接ロボットの存在するエリアの配置方法および廃止による別ロボットへの作業割り当ての修正・溶接ガンの改造検討なども実施。
生産量が減るために不要な工程の削除や移設先のエリアに合わせたライン形状の変更などの検討、およびそれにかかわるライン改造の仕様作成と工事管理も実施。
作業デッキで覆われた古いロボットラインがあり、解体してみないと設備の設置状態自体がわからないものもあり、解体しながら移設資料をまとめるなどの対応も必要であった。
ピットが存在した設備について床上に置けるように設備の改造も検討・仕様作成・改造指導。
安全対策の改善のための検討・仕様作成・工事指示・結果確認も実施。
現行ライン停止から再立ち上げまで3か月で予定通り完了した。
様々な内径の金型をマガジンにセットし、自動にて金型をマガジンから取り出し、計測器にて内径測定後、任意に設定されたコンテナに振り分ける装置。
要求仕様に沿った設備計画、設計。
部品製作・組立・試運転・搬入・据付までを遂行。
測定精度が1μm、仕分け精度10μmを満足する計測器の見極めが必要。
処理能力15秒/1金型を満足するシステムの計画。
多品種対応によるタッチパネルでの仕分け設定。
製作仕様書、機械組立図、空圧系統図、制御盤外形図、展開接続図、シーケンサラダー図、取扱説明書(運転要領書、機器リスト)、打合せ議事録、全体工程表、他
要求されたスペックの自動機を納入完了。
1直1万箱におよぶ多品種生産を行っている工場において、プレスライン~中間貯蔵庫~パレットへの自動積載~出荷レーンへの搬送を自動化するもの。
AGV、高密度高速自動倉庫、ロボット自動パレタイジング、コンベアを組み合わせ。
複数の生産管理システムから来るオーダーを統合して生産・出荷をコントロールするWMS/WCS。
IDによる箱の個別管理と箱に対する出荷カンバンの自動取り付け。
中間搬送をAGV化するためのプレスラインコンベア改造。
各出荷パレットに対し、部品種類・箱数・箱サイズ(2種)がランダムにオーダーされるため、倉庫からの切り出しは箱1つ1つをパレットにどう積むかを見込んで順列で行うことが求められる。
将来の能増や対象部品転換を見込んだ、高速で入出荷する多品種部品を生産ロットの混在も防ぎながら賄うための倉庫容量の適正値の算出。
複数のプレスラインへの空箱の配送、実箱の集荷を一括したAGVシステムで行うための適正台数の割り出し。
トラック集荷時間に偏りのあるパレット出荷場の必要レーン数割り出し。
ID化による生産カンバン廃止と手作業を前提とした出荷カンバン取り付けの自動化。
新プレスラインの導入も含めた手作業から自動化へ移行するための改造スケジュール。
検討条件サマリー、AGV台数計算、倉庫容量・能力計算、ロボットパレタイジング能力計算、出荷レーン能力計算、空箱集荷能力計算、WMS/WCS構想書、レイアウト、各設備仕様書(新規・改造)、改造スケジュール、設備投資見積、報告書
課題をクリアする計画は構築できた。投資削減のための運用における課題も見えた。
自動車部品生産設備、および設備間に接続するユーティリティーの配管ルート図を作成。(4万平米)
数種のエア、給水、冷却水、数種類の蒸気、オイル、高圧作動油などが対象。
バルブやトラップなどの配置検討も含む。
この検討後、現地で2年にわたり配管工事の管理も遂行。
流体条件により、現地調達できる妥当な材料を選定。
工場側の消火配管やダクトとの干渉を避け、防火セクションに区切られたエリアを通過するなど、運用条件に見合う配管計画。
優先順序を決め材料調達・プレハブ工事を遂行。
建屋側工事・機器設置工事・運転とのスケジュール調整をしながら、上空・立下げの工事をタイミングよく差配。
高圧油圧配管は部分的に輸入材を手配し、溶接検査、耐圧・リーク検査も適正に手配・管理。
設備側も含め、適宜追加工事の仕様作成・施工管理を実施。
配管材現地材料選定表、配管ルート図(ルート、サイズ、バルブなど機能要素配置、支持方法)
工事スケジュール、検査基準、個別工事指示書
設計に基づく日本側標準に見合う現地工事の完了。
2直年産8万台、自動車車体溶接工程のボディーサイドインナーRH/LH生産ライン。
ロボット17台。スポット溶接、ハンドリング、シール塗布自動化。
レイアウト検討、設備仕様(治具、溶接ガン、ハンガー、台車)作成。設計・製作確認、設置監理。生産開始までのライン立ち上げ支援。
一般的な生産技術が行う作業を、プロジェクト開始から生産開始まで一貫して支援した。
展開エリアに制限があるため、より効率的な機器台数による生産工程を計画し、ロボットの動作、作業エリアを集約する事でレイアウトを成立させる。
既存設備の生産終了日程を考慮し、仮設置にてシステム連動確認、旧設備撤去後に本設置を行うなど、プロジェクトの日程管理が要求される。また、一部遊休設備を流用し、全体の投資コストを抑える様に計画する。
製品データ確認、形状変更要望書。
工程計画(レイアウト、時間検討、作業検討、機器リスト、作業指示書)、工程設備仕様書(治具、溶接ガン)動力、安全エリアマップ。
ポカヨケマップ、ロボット成立性3D検討、ロボット手首負荷計算、溶接条件表、全体日程表、設置要領書
工程I/O確認、設備機能確認、単動/連動確認シート、ティーチング用ワーク作成、NPチェック、設備能力確認、他。
本業務結果をユーザーに引き渡し、ユーザー側で計画通り新ライン立ち上げが完了している。
輸送機器保全用大型構造物(7階建て相当)の2D設計をエンジニアリング会社が行ったが、設計ミスの発見、重量計算など2Dのみでは確認が難しい項目があった。それを3D設計化することにより確認する業務。
2D単品図面および2D総組図を基にして、部品ごとに3D CADデータを作製し、組み上げた。それらのデータについて不成立な点を3D図にて確認してフィードバックを行なった。
またすべての部品の重量を算出しリスト化。エンドユーザーの重量要求を満たしているか確認した。
総組状態での全体の重心位置についても計算しレポーティングを行なった。
また、輸送機器に対し構造物を配置した状態での干渉および可動式ユニットの固定位置を確認し、設計に反映すべくフィードバックを行なった。
3Dデータ、重量リスト、2D図面不具合レポート、重心情報、輸送機器との干渉確認結果レポート
設計のバックデータおよび製作の参考データとして活用。
デパレタイザー/パレタイザー、保管用自動倉庫(パレット単位、箱単位)、順立て用シャトル、有人工程振り分け用コンベア、出荷前ストレージ用自動倉庫などからなるシステム。
非常に多くの製品(約1万箱/直、約8千種)を扱う倉庫であるため、効率的な格納方法、入出庫方法の実現のために様々な調査・検討を行った。
現状のオペレーションでの問題点(重筋、無駄作業、人手がかかる作業など)を洗い出し、分析。
多品種対応として、倉庫への格納方法を複数用意し、出荷箱数や頻度によって使い分ける方式とした。
また、自動化率高・中・低の3段階の計画を立案、それぞれの概算投資と品質上の優劣を明示し、客先により選択できるようにした。
製品を入れる通い箱のID管理が求められたが、使用後の洗浄作業があるため、条件に適した認識手法を実験により求め、提案した。
仕向け先ごとに出荷形態が多岐にわたるため、各種自動工程と有人工程をフレキシブルに結びつけることのできる搬送方式を選択した。
現場調査結果の分析レポート、自動化アイテムの提案、自動化率別プロセス構想、倉庫容量・能力計算、ロボットパレタイジング能力計算、箱ID管理構想書、レイアウト、各設備仕様書(新規・改造)、設備投資見積、報告書
倉庫建設のベース資料として完成。
コンベアによる流れ作業を行う工程で、いくつかの危険ポイントがあり、それに対して有効な安全装置の導入を行った。
ライン途中に存在する重量物高速搬送機前後の工程の作業者との干渉防止。
上空から大物の部品をインラインで下降させるドッキング工程での落下可能性エリアへの作業者侵入検知。
コンベアの先端での作業者巻き込み防止。
コンベア終点での次工程コンベアへの着地前挟み込み防止。
その他、塗装パワーフリーコンベア間の送り込み装置による挟み込み防止対策。
自動車会社で行われている安全対策レベルの実現。
何が危険要素かの見極め。
現行ラインのエリアの拡張はできない状態で、工程の削減もできず、現状の作業エリアと作業配分を維持したまま、作業の危険性を排除することが必要。
安全対策が急がれるため、できるだけ簡易な改造での対応。
作業者の動線、多品種の製品と干渉しない安全装置の計画。
現場調査および安全対策構想、改造仕様書、メーカーへの説明、見積内容の精査、図面確認、工事日程調整、工事立ち合い、稼働確認。
当面の重要危険減の排除を達成。